We use thread gauges to check all cooling threads.
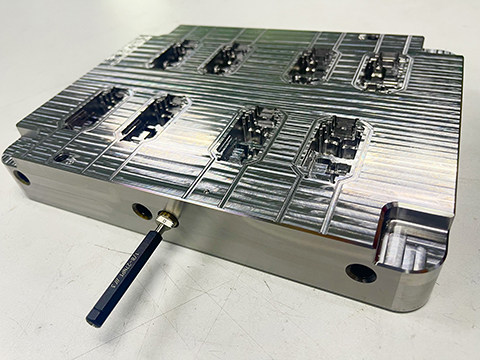
RFQ
Feasibility Study
Quotation(Including simple part analysis)
Price confirmation, PO from customer
Project Kick Off
DFM
Mold Flow Analysis
2D/3D Mold Designing
Design Approval
Mold Machining
Tooling Progress report Every Monday
Tryout Resins Prepare
Fitting
Mold Tryout
Mold Improvement And Engineering Changing
Approval of Mold Shipping
Packaging&Shipping
After-sales Service
In the manufacturing process, we place greater emphasis on quality than many of our peers. Since the year of 2010, all the cooling water threads of the molds we manufacture have been machined by CNC and 100% passed thread gauge inspection. Our inserts and ejector pins are all cut by precision slow wire cutting machine, eliminating the need for manual repair work, and achieving an accuracy of 0.002mm. Every Monday, our project engineers will update customers with the latest progress report.
We use thread gauges to check all cooling threads.
We use a maximum 135x, high-definition industrial 4K microscope to inspect mold details.
PW uses scientific injection molding method for mould trials, to help customers find the optimal injection parameters and quickly put them into production within 6 steps.
Confirm whether the installation dimensions of all molds such as nozzle R meet customer requirements.
Check for steel residual in the cooling channel using a fiber optic microscope.
Before shipping the mold, we will disassemble the entire mold, carefully inspect each part, and take photos to make record.
Confirm if the ejection action is smooth and record a test video.
Doing a good job of rust prevention for the mold. According to different customer requirements, anti-rust spray or mould grease etc. can be used.
Check for any water leaks during transportation.